Trusses are diagonal connectors in any structural support. If you have ever seen bridges, you will often see that there are extra diagonal metals that run along with the basic metal structures. The entire combination of these diagonals forms what are called trusses.
They are not only common in bridges but are found in things as basic as fire brigade ladders. Trusses can be for many purposes. Some common ones are the stage truss, ladder truss, roof truss and Lighting Truss.
Types Of Trusses
Trusses can be of multiple types. They are constructed for the purpose of support systems. Therefore, different shapes, joints and bends might be needed for every different kind of structure. It is upon the architect to decide which combination shall work best for the project and in the most feasible manner.
Some renowned types of these connectors are:
- Warren
- Camelback
- K-Truss
- Lattice
- Howe
Each of them has a unique flexibility that they can provide. In some situations, it is ideal to opt for a cable-based truss. These cables can be forged from a variety of elements or compounds. More often than not, bridges use them. The Sydney Harbour Bridge uses the arch to provide stability, while the metal arch is supported by “N” shaped trusses. Even in the case of the London Bridge, we can see these connectors all the way up. They are also connected to the cables that hold the roadway.
What Should Be Considered Before Choosing One?
1. Strength
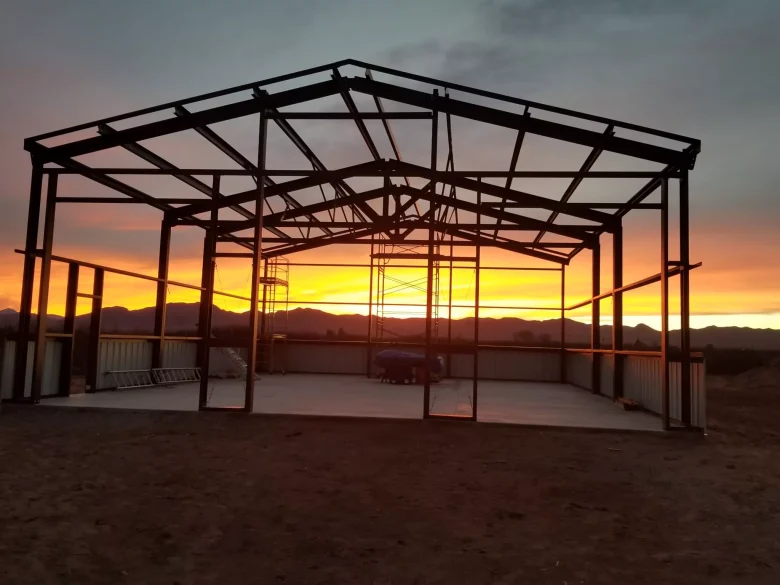
Aluminium is generally much lighter compared to iron. Aluminium is definitely not as formidable as iron, but it becomes sturdier if combined with another metal to form an alloy. It is never ideal to go for pure forms of either metal. Iron is incredibly firm and will almost support heavy weights. Therefore, if the requirement is such that it specifically demands to have high tensile strength, going for iron is not a bad idea.
On the other hand, aluminium provides lesser strength in its pure form. It is convenient for building unconventional shaped stages or roofs. The same weight of aluminium in its alloy form is much stronger than iron. It implies that if both metals are taken in equal masses, aluminium will surely provide much more strength.
2. Malleability
One may consider aluminium if the requirement is for custom trusses for absurd shapes and dimensions. It is a lot easier to customise the style of roof or shape of the stage. Malleability means the ability of a metal to bend. Even in film sets, we often require aluminium trusses to receive maximum flexibility in choice.
3. Durability
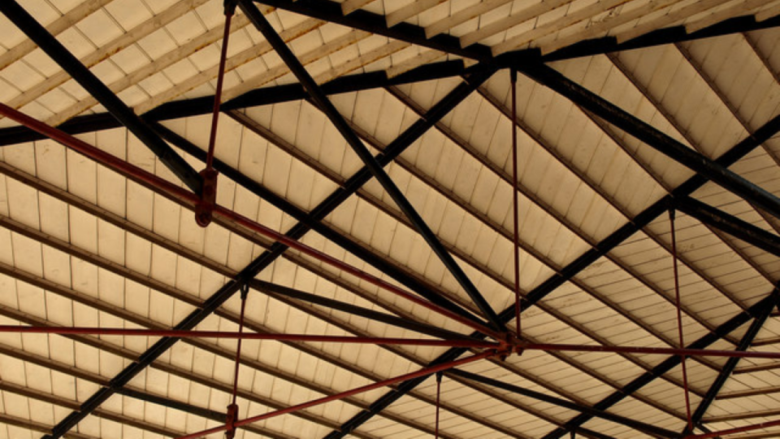
Aluminium is supremely durable. Iron is known to rust easily in wet conditions. Even with a hydrophobic coating or paint, iron gets scraped off easily in time and therefore rusts. The strength offered by it is therefore compromised. The former, on the other hand, is extremely durable in the long run. Aluminium is, however, susceptible to corrosion from chemicals and acidic material.
An aluminium truss often supports roofs. These are a better option because they can sustain rain and heat. A roof is prone to extreme weather conditions like heat, snow, rain and strong winds. This type of harsh weathering will break down iron a lot faster. Iron is conversely exceptional against strong winds. It will remain affixed in its place and will ensure that roofs do not fall apart. Aluminium is lighter and will be shaken by high speed winds.
4. Heat Resistance
The heat resistance to be considered here is not from the sun or lights but from factories where it is common to achieve temperatures in excess of five hundred degrees celsius. Iron has a higher melting point. It can withstand the tremendous pressure from such factories, whereas aluminium tends to fall apart. It will turn soft, and the entire architecture might lose support from these trusses.
5. Costs
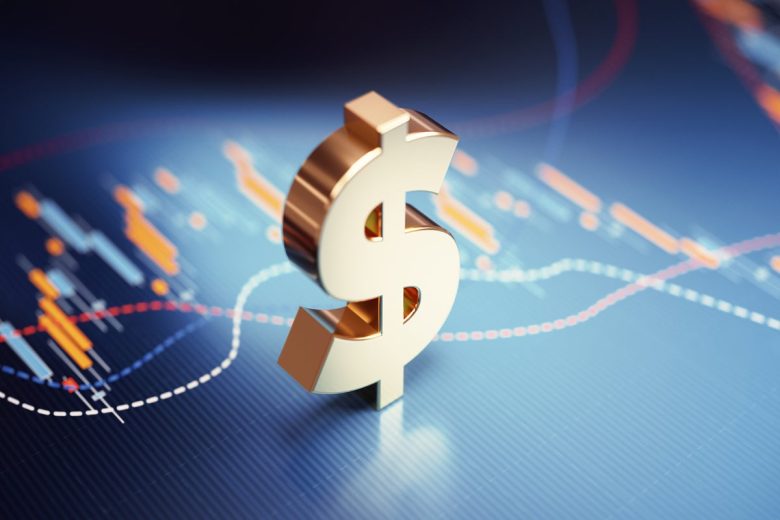
Cast iron is relatively more expensive. Thus, it renders Its purchase and uses for a high a budget project. On the other hand, if we compare a uniformly coated aluminium truss system, it might be a tad costlier.
The maintenance costs are often ignored. Both of them require you to incur expenditure to renovate and repair. But iron normally wears out almost entirely. It will last longer if it is in the form of an alloy like steel. But pure iron is going to cost a lot. Especially after the pandemic, iron and steel prices have been on the rise. It is not as feasible to get iron trusses.
6. Transport
Iron is obviously the heavier of the two metals. This factor implies that it is not easy to transport it. Not only does it make it more expensive, but also inconvenient to transport over long distances. For major projects, it is still possible. Still, for events like shows and performances where stages are set up temporarily only, it becomes incredibly difficult to carry it along everywhere there is a show.
Moreover, the entire trusses need a lot of human resources or machinery to set up if they are made up of iron. In the case of aluminium, they can be carried around by manual labour. This feature is the reason why film shootings often utilise them.
Conclusion
It can be either of the two trusses that you may select. What is essential is that you need to have a better understanding of what your requirement is. In a situation where a stage is to be constructed for performances, shows, rallies, speeches or other events, it is ideal for giving the fundamental support as iron, and the rest can be the other metal. In this way, you can secure the best of both worlds.
For large architectures like buildings, bridges and monumental factories, it is never advisable to go for the lighter metal of the two. However, if specific needs are such that they require the use of the lighter one, you may.